Seemingly random inverted signal
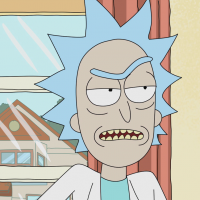
nezzreth
✭
in RobotStudio
Of the 30 or so ABB robots at my plant, maybe once or twice a month a random DO gets inverted and therefore stuck ON.
A warm-start always fixes the issue but on certain machines it's more common.
Does anyone know how or why this would happen?
Could it be some weird interaction with a PLC?
Does it have to do us using the pulse instruction?
A warm-start always fixes the issue but on certain machines it's more common.
Does anyone know how or why this would happen?
Could it be some weird interaction with a PLC?
Does it have to do us using the pulse instruction?
Tagged:
0
Answers
-
It is properly the pulse command.The pulse command inverse the status of the signal.
Regards
Knud Erik Lindberg
Jorgensen Engineering0 -
I know that the PulseDO instruction inverts the signal.
What I want to know is why does the signal sometimes stay inverted after a pulse of a few seconds.
When the pulse ends, the signal should revert back to its original state.
That happens 99.9999% of the time.
I'm looking for the answer about the other 0.0001%0 -
Maybe too long ago now, but I use to have the same problem with a conveyor, which was stopping instead of starting at a certain 'pulseDO' command. Totally arbitrary, because the next day it would function fine. I solved this by adding some extra arguments to the PulseDO: PulseDO\High\PLength... In this case you're sure that you will always have a 'High' pulse instead of a signal going low... The reason why.... I still don't know.0
-
As TME said, might be an old thread, but people might still have problems with this.I've noticed that the PulseDO seems to lock the signals state if the program execution is stopped while the signal is high. Therefore, I always use the /high parameter when pulsing signals (so it won't get an inverted pulse) and at startup I always use an init function to set all the affected DOs to 0.Personally I rarely use pulses due to this, only in cases where a locked high signal won't create any problems.TME said:Maybe too long ago now...0
Categories
- All Categories
- 5.6K RobotStudio
- 401 UpFeed
- 21 Tutorials
- 15 RobotApps
- 303 PowerPacs
- 407 RobotStudio S4
- 1.8K Developer Tools
- 250 ScreenMaker
- 2.8K Robot Controller
- 353 IRC5
- 74 OmniCore
- 8 RCS (Realistic Controller Simulation)
- 850 RAPID Programming
- 25 AppStudio
- 4 RobotStudio AR Viewer
- 19 Wizard Easy Programming
- 110 Collaborative Robots
- 5 Job listings