Gas shuts off while welding
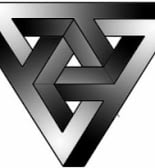
Thanks,
IRB2400
s4c+
Comments
-
in the video below it shows that the gas actually shuts off within a couple seconds of welding and then thats when i get the "arc supervision signal" fault. i know its hard to see but that led light that is on first at the beginning (LED Output Light #2) is the gas signal. its also the light that shuts off first.https://m.youtube.com/watch?v=zNtNJQW5QTY
taking a look around the motherboard cubicle i noticed that i dont have the gas signal sensor wire even hooked up, is this something that i absolutely need or is there someway i can get around it?
Thanks
Beau @ SureFab0 -
Hi Beau,
Im not sure if you have made any headway with the fault or not but I might be able to give you a few things to check. I have seen this error previously but It can differ depending on what type of equipment you are using.
Normally an arc supervision error is caused by a faulty signal back to the control informing it that an arc has been established I would definitely check your documentation for such an input. This input may not go to the robot controller but instead to the interface or regulator boards in the weldset. I would say that the gas turning off is just a knock on of this.
It might be worth checking that the weld return path is sound as high resistances on the return have been known to cause supervision errors. As for the gas sensor being removed I wouldnt worry too much, especially if it has been like this from day one. I myself have always seen them in use as unmonitored changes in gas flow can cause porosity / defect.
What weldset are you using ? esab, aristrob, fronius ?
Im sorry I cannot give you a concise answer but supervision errors are quite general errors.
Thanks
Chris
0 -
Hello Chris,
I have not made any headway yet. im hoping today will be that day. This video may not help much but this is whats happening on the AWC.in the video below it shows that the gas shuts off within a couple seconds of welding and then thats when i get the "arc supervision signal" fault. i know its hard to see but that led light that is on first at the beginning (LED Output Light #2) is the gas signal. its also the light that shuts off first.https://m.youtube.com/watch?v=zNtNJQW5QTY
I fixed the gas sensor issue as well. for some reason it was linked in with my water flow sensor on the chiller. the motor on the chiller was seized up so it was sending a low signal back to the interface.
for weldset im using a Lincoln Invertec PowerWave 450, esab .052 solid wire, argon gas set around 35-40 psi that i checked at the nozzle. and on the robot end its Adcanced Weld Controller.
weld schedule:
27.5volts
240 amps
6.0 Meters/min wfs
Thanks0 -
Beau,
Unfortunately I am not very familiar with the Lincoln sets,
I have seen the gas and water meters linked together a few times, they are normally in series so that both have to be healthy in order to continue.
I have watched your video, its very difficult to see the timing but Im sure you are correct. Have you tried a spare weld set (if available )
Also do you have access to the wiring diagrams for your setup ? there are so many variations its almost impossible to fault find without the correct set
Thanks
0 -
Chris,
I dont have a spare welder available unfortuneately... i have been searching for these wiring diagrams but am unable to find them at the moment... is their some sort of cross
connection i am able to do to keep the gas on?? i have a feeling i have some sort of I/O configuration that isnt correct. i forgot to mention that i just started working on this
robot. and havent been able to get it to make a single weld yet.......0 -
To clarify is the output to shielding gas that is turning off?
You can manually force this on in the I/O window.
The arc supervision fault is due to the fact the robot has not received back from the welder a high signal on the input 'arc established' within the set time period.
This could have been because of the gas/water flow switches which are normally part of the welder control (not the robots), if you have fixed the flow switch issue is it all now working?
0 -
Yes, it is the output to the shielding gas.. i have traced back the wiring as well and the relay for the gas also flips back to the off position first with the wire feed forward and arc establish relays to follow a second after.
I have also tried to manually force the gas to stay on but still throws the same fault code and the relay flips on and off rapidly until i go back to the I/O menu and shut it off..
could it be possible that the AWCGaWr (gas/water) signal is not set to the right input? does that have anything to do with it?
by the way i have found the wiring diagrams as well
,Thanks for the help so far.0 -
Are you getting a system that has been in storage/not used for a while running again - or was the system running and has just come up with this fault?
0 -
Yes, i am using a system that has not ran in over 4 years..... i feel as if the robot set itself back to its default I/O settings... its almost like the AWC isnt synced up right with the default I/O board.
also im not sure if this makes a difference but i have an analog volt sensor and amp sensor. when the robot trys to weld i dont get a reading on the teach pendant from either of them....0 -
If you are not confident that the I/O is mapped correctly that could be the reason for not seeing the amps & volts.
You should put a meter on the signal coming into the controller from the sensors to ensure the sensors are working.
I am not familiar with the AWC system but it sounds like all signals are coming back to the robot controller which is doing all the logic for the welding system (today the robot controller simply asks the power source to turn on using weld schedule xx, and the power source reports back that the arc is established or not) - so if the robot controller does not see any voltage or current in the weld system after it has started the welder it will stop the process with an error -> which is what you are seeing.
0 -
****Problem fixed****
Had ABB Come for a week and I ended up having a corrupt .plc file that syncs the robot and the welder together0
Categories
- All Categories
- 5.6K RobotStudio
- 400 UpFeed
- 20 Tutorials
- 15 RobotApps
- 301 PowerPacs
- 406 RobotStudio S4
- 1.8K Developer Tools
- 250 ScreenMaker
- 2.8K Robot Controller
- 350 IRC5
- 74 OmniCore
- 8 RCS (Realistic Controller Simulation)
- 848 RAPID Programming
- 22 AppStudio
- 4 RobotStudio AR Viewer
- 19 Wizard Easy Programming
- 109 Collaborative Robots
- 5 Job listings