Palletizing PowerPack
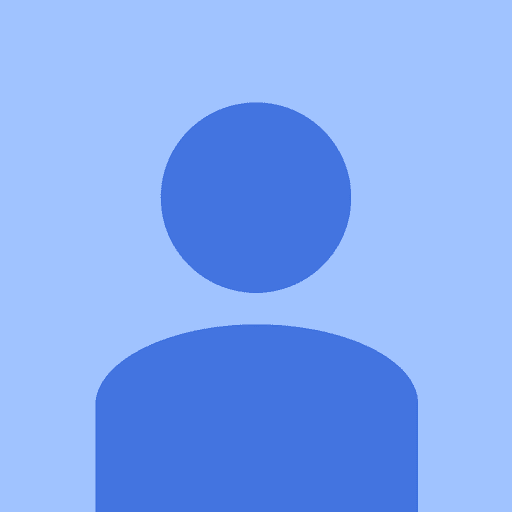
We are working on 2 palletizer projects, for one of them we are waiting for the robot to arrive.
We started to study the power pack manual, we also done a simple simulation in RobStudio, but i cant manage to find 3 things:
- variable DropHeight for specific items in a layer
- the client wants to place an outer ring of bags on the pallet to 10mm to the previous layer
- then in the inside of the ring we can drop the remaining bags from 150mm height, due to Gripper claws opening collision with the other bags
- client wants the outer ring of bags to touch the previous layer (10mm) so the stack will be more uniform
- variable Place PalletPattern
- in the Add/Edit Job at the end when you select the OuterFeeder layers, you can modify the approach medthod (Drop, Left...) but i cant manage to change the order of the bags from the automatic order (1, 2, 3, ...)
- we want to change the order of the placement so we can create that outer ring of bags that we approach the previous layer to 10mm, to put them in a logical order so we dont have Gripper claws collision with the previous placed bags in the current layer
-New "recipe" creation without RobotStudio
-our client asks us to implement an easy and cheap method of creating new "recipes" (new Bag dimensions, new pallet patterns...)
- is there a way to do this outside of RobotStudio, and without robot programming knowledge?
Thank you for your time and suggestions, any suggestions would be great as we are just starting to work with these power packs, and if we get the hang of it we will start suggesting them more and more to our clients.
Comments
-
Hi
I will try to help you out with your questions.- The variable drop height can only be set per layer, not per individual product. It may be considered in future development if required.
- There is a possibility to edit the placing order at the last stop of the Job wizard and also when you edit the operation set from the tree view. You basically just edit a layer and start to remove a all or the last placement and redo it.
- All recipe additions or edits must be made from RS+PzPP but there is no requirement to purchase premium license for that purpose. Basic license is enough for adding and editing new products and patterns
/Mats0 -
Thank you very much.
Really on point answers.0 -
Hello,
After some simulation and documentation time with the power pack, we started to work with the real robot. After a while i managed to get the Palletizing Pack to work with our automatic cycle controlled by the PLC, but i encountered some more questions, i solved some of them but im not sure if i used the best use case for the problems.
Description:
- 1 gripper for 1 product
- 1 infeeder, 1 product at a time, 2 types of bags in total
- 1 outfeeder, pallet fed by conveyors , n types of patterns
PP configured as:
- 1 project
- 1 flow that autostarts (i dont stop and start this inside my plc code)
- 1 infeeder and 1 outfeeder
- inside the flow we have the n palletizing patterns configured (2 for now), based on the selected recipe we give the master outfeeder a job with the wanted palletizing pattern
Questions:1. wait over infeeder/outfeeder if there is not yet product or pallet present
--how can we configure the project to approach the infeeder position even if there is no new product there, but for sure the next job will be a pick job when the bag arrives
2. MoveHome routine
-- at station initialization, how can we trigger this routine without the infeeder loosing hes memory that the robot has already picked up a product and is ready to place it?
3. discard bag from gripper
-- what is the correct way to discard a product from gripper automatically in case we initialize the station and we dont want the gripped product no more? (after a project restart, maintenance, recipe change ...)
-- we have a designated area to place the unknown bags but coudnt figure out where im supposed to write the movement logic
4. gripper init and handling
-- where and how do we handle the gripper logic from the Event numbers to actual digital IOs? how is this connection supposed to be set up? I am using the tool event numbers 1 for the gripping of the bag, and 2 for the fixing cylinders
-- those integers can have the value 1 or 2, but with these values i should activate and deactivate 2 digital outputs wired to the robots IO card, is there a place or procedure on how i should do this? (all gripper digital IOs are wired streight to the robot controller)
-- for maintenance reasons we need to have a manual control on the gripper functions, open/close the respective cylinders, how is this handled in the PowerPack or where can we write our own logic?
5. write aditional logic in robot
-- where can we as users write additional logic in the robot? (ex: gripper check in move home sequence, bag discard in move home sequence, directly approach infeeder after place is completed, approach outfeeder after pick is completed, gripper handling in manual mode/ digital IO conversion linked to the integers used as tool Events)
-- is this possible or the Palletizing PP is not supposed to be modified at all? I tried writing some code but noticed it disappeared after a project restart, then I found out the source of the project in the folder structure and modified there the MoveHome routine but this was also deleted once I redownloaded the project configuration from RobotStudio
6. example project
-- an example project with Siemens PLC integration would mean allot of help (TIA or old Step7), or even some logical flow that we should follow in using Project/Flow/Feeders, both in normal running conditions but also while resetting the project from different scenarios
-- im sure that there are intended solutions to the above described questions, after all they are pretty common topics in a robot integration, for me its just not clear what they are only based on the documentation, the tests we did so far, my experience
-- our cycle works in expected working conditions but these NOK and maintenance topics give us a hard time to solve
Thank you very much for your time.
0
Categories
- All Categories
- 5.6K RobotStudio
- 401 UpFeed
- 21 Tutorials
- 15 RobotApps
- 303 PowerPacs
- 407 RobotStudio S4
- 1.8K Developer Tools
- 250 ScreenMaker
- 2.8K Robot Controller
- 353 IRC5
- 74 OmniCore
- 8 RCS (Realistic Controller Simulation)
- 850 RAPID Programming
- 25 AppStudio
- 4 RobotStudio AR Viewer
- 19 Wizard Easy Programming
- 110 Collaborative Robots
- 5 Job listings