Using robots as generators

tsharma1
✭
in RobotStudio
Hello Everyone,
We have two IRB 7600 ABB Robots in lab facility and we are doing an experiment where the robots are coupled face to face using a fixed coupling (with additional flanges and screws).
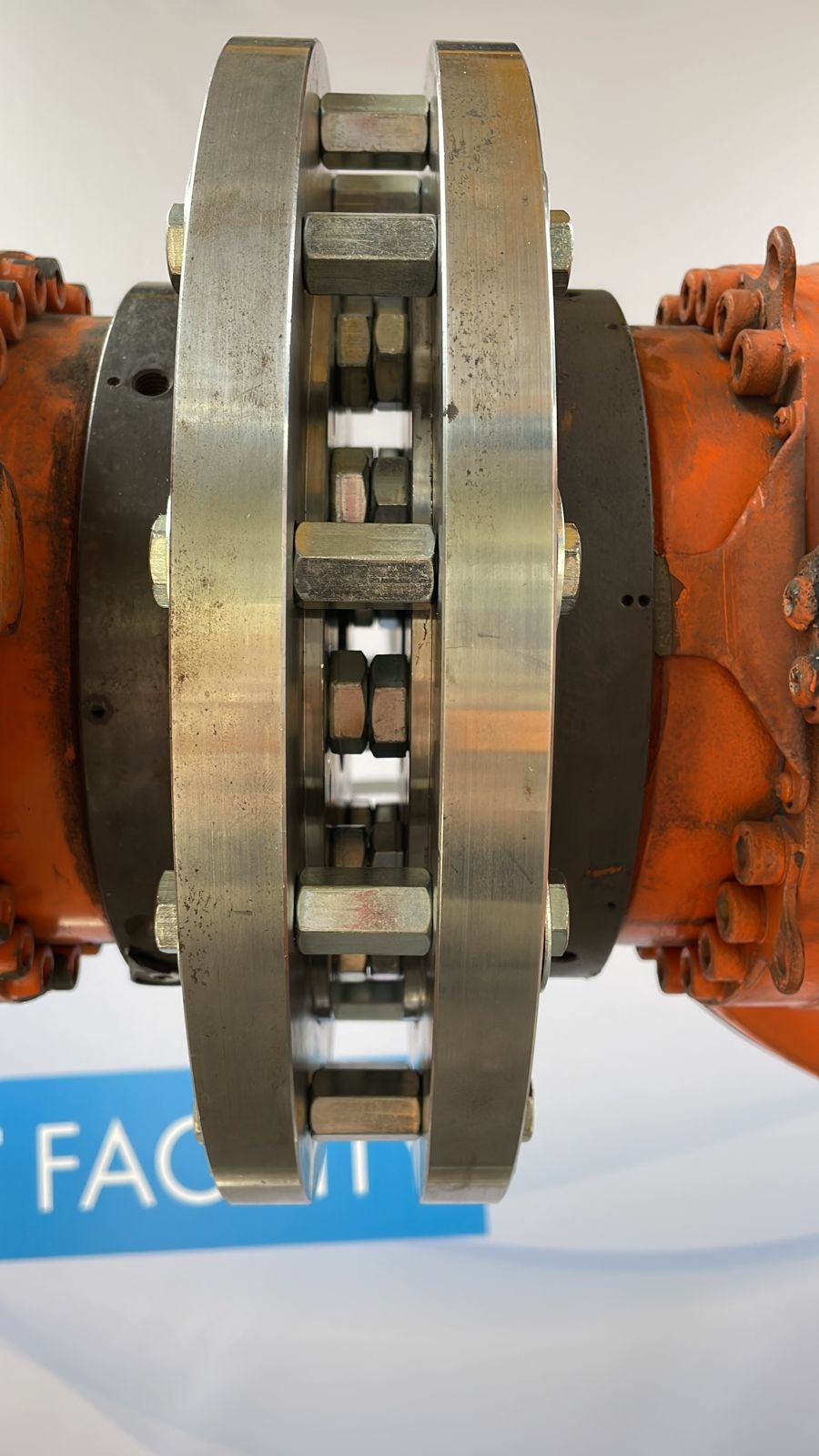
One robot say B is acting as a manipulator doing the regular robot operation while other one say A is used as generator. Robot B is connected with IRC 5 controller and a 24 volts supply is connected to release brakes on Robot A. Robot B will push or pull the robot A and the voltage will be generated. For now we are only focusing on the movement of axis 2 and 3 for voltage generation.
We have programmed the robots in such a way that only arm 2 and 3 moves in the manipulator. We are using MoveJ instruction. I have tried to draw the step by step movement of the robots.
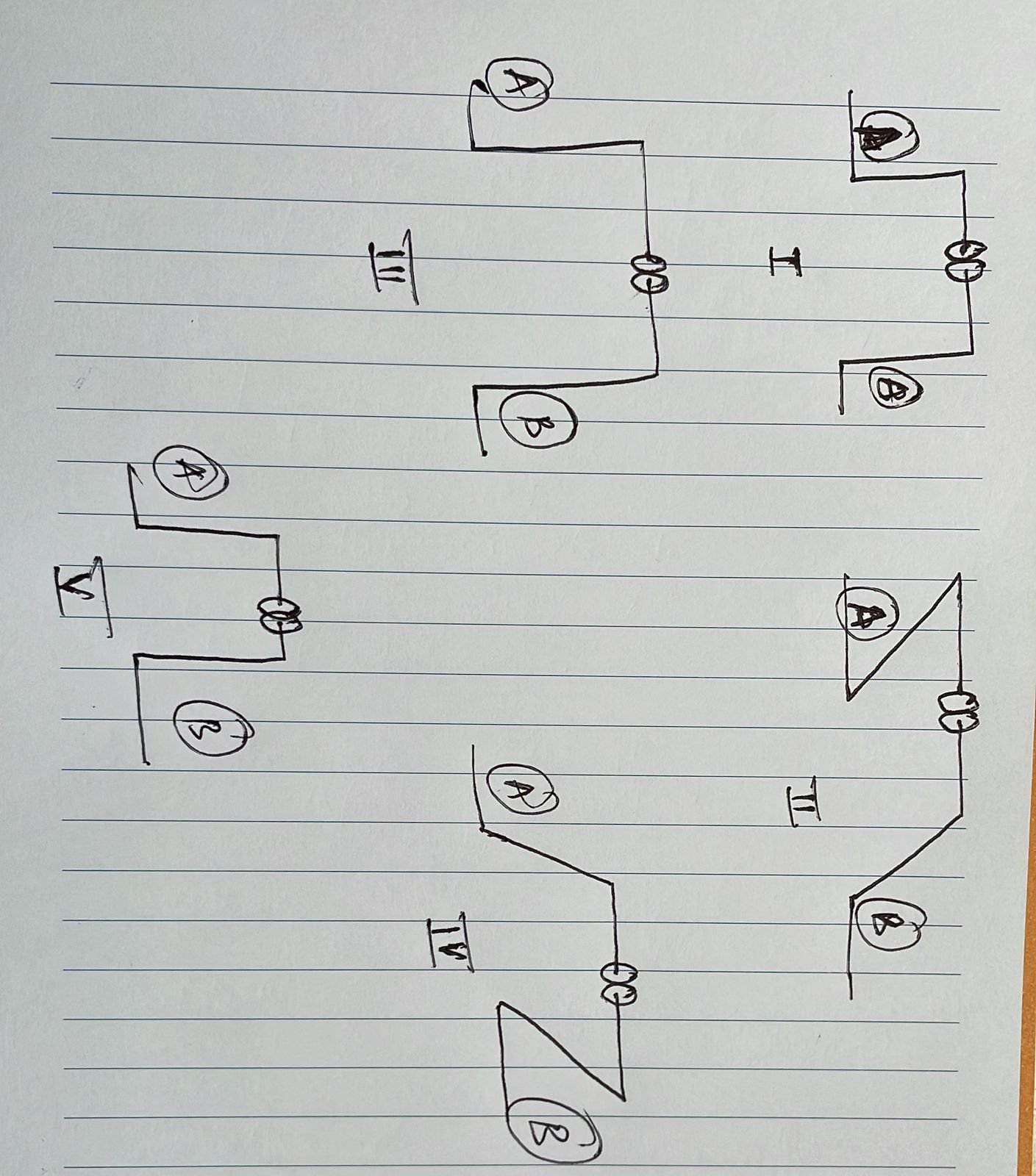
Position I, III and V are basically the home positions. However while moving the robot A with robot B, we could only achieve position II. In the case of going to position IV controller (robot
gives an error of Motion Supervision (50204) and sometimes Joint Collision (500056). Also, the position II can be achieved at low speed upto 150mmps. As we invrease the speed to 200 mmps the same error occurs.
WE DO NOT HAVE ACCESS TO ROBOT STUDIO AND ARE PROGRAMMING USING FLEX PENDANT in REAL TIME.
I guess the error is due to the incorrect load definition. As the generator robot is like a tool to the manipulator robot and we did not define any tool. We just used default tool0. I went through some tutorials on youtube for defining tool and followed the procedure. But it ask for the mass, center of gravity and I am not sure about what to put in those values.
Still, I am wondering if this is the issue then why I am able to move the robots at low speed.
If any of you can help me in this regards then it will be great help.
Thank You!
We have two IRB 7600 ABB Robots in lab facility and we are doing an experiment where the robots are coupled face to face using a fixed coupling (with additional flanges and screws).
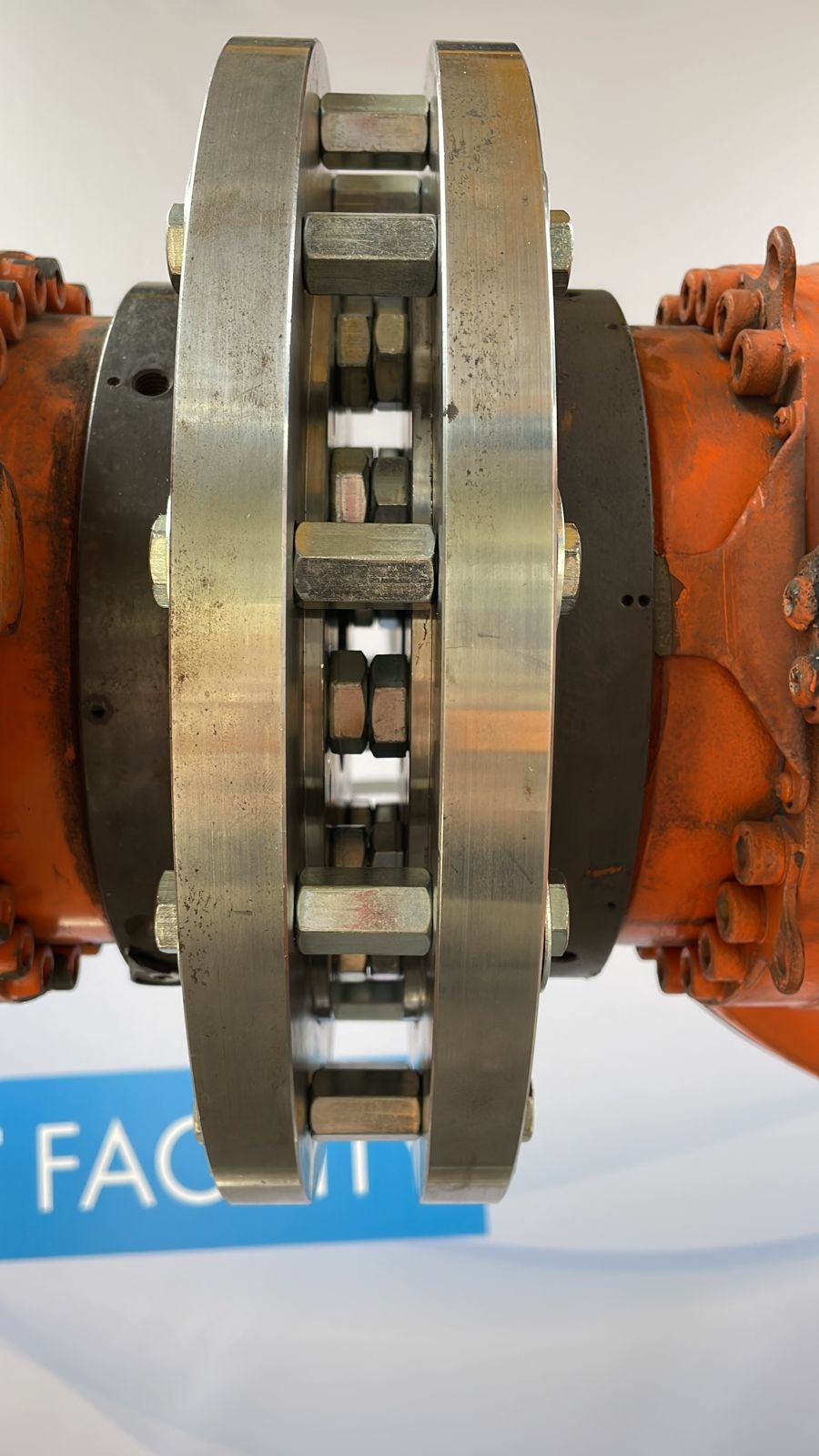
One robot say B is acting as a manipulator doing the regular robot operation while other one say A is used as generator. Robot B is connected with IRC 5 controller and a 24 volts supply is connected to release brakes on Robot A. Robot B will push or pull the robot A and the voltage will be generated. For now we are only focusing on the movement of axis 2 and 3 for voltage generation.
We have programmed the robots in such a way that only arm 2 and 3 moves in the manipulator. We are using MoveJ instruction. I have tried to draw the step by step movement of the robots.
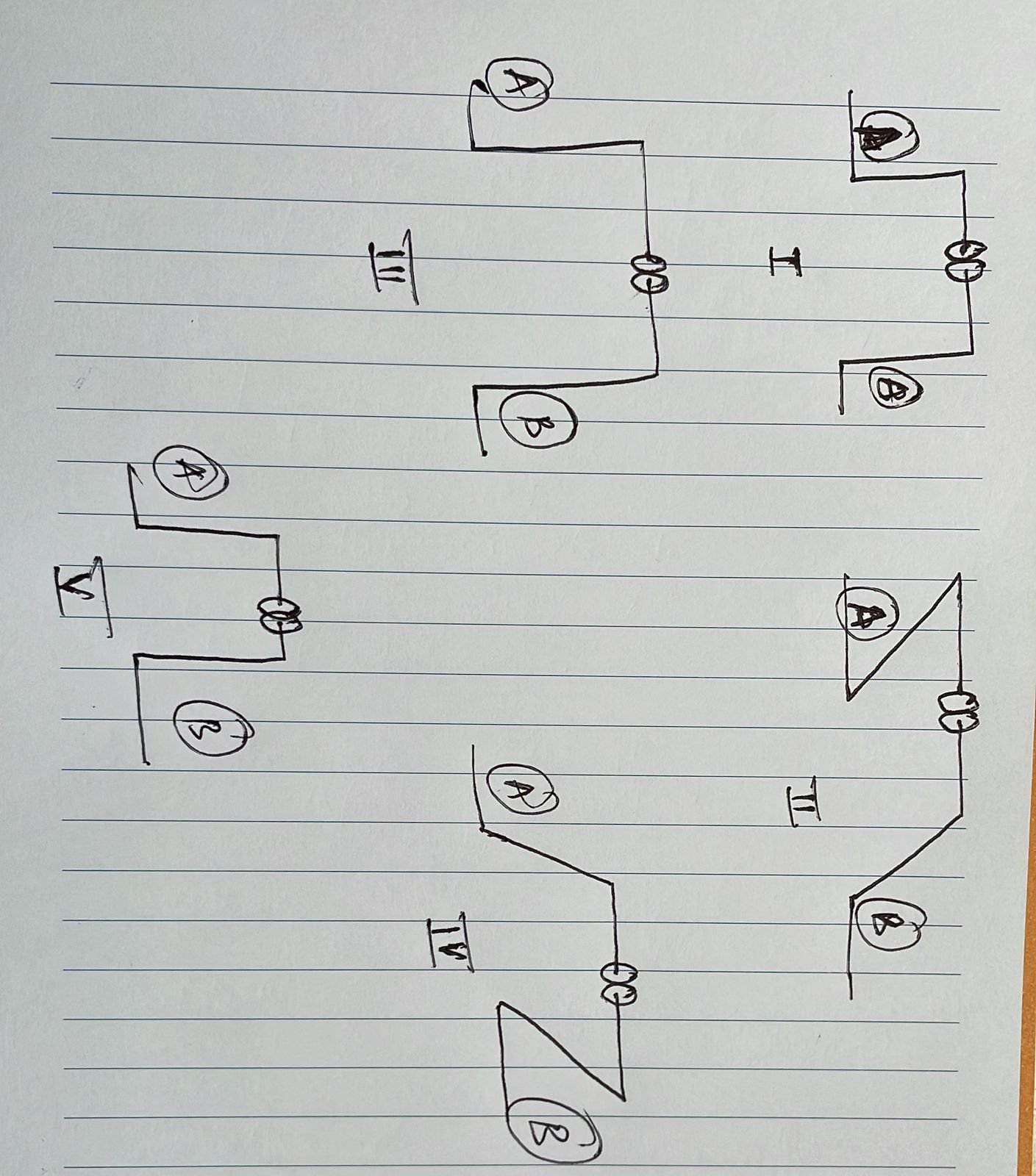
Position I, III and V are basically the home positions. However while moving the robot A with robot B, we could only achieve position II. In the case of going to position IV controller (robot

WE DO NOT HAVE ACCESS TO ROBOT STUDIO AND ARE PROGRAMMING USING FLEX PENDANT in REAL TIME.
I guess the error is due to the incorrect load definition. As the generator robot is like a tool to the manipulator robot and we did not define any tool. We just used default tool0. I went through some tutorials on youtube for defining tool and followed the procedure. But it ask for the mass, center of gravity and I am not sure about what to put in those values.
Still, I am wondering if this is the issue then why I am able to move the robots at low speed.
If any of you can help me in this regards then it will be great help.
Thank You!
0
Comments
-
I think you can disable motion supervision, but a Joint collision is a much bigger problem, because the joints are going above their torque limits, it seems.How is the state of robot A? Brakes on or off? There is an instruction called SoftAc. This sets an axis to a soft mode. You could try that, but the robots are definetely not made for such an experiment.Also for the mass and mass center, this is tricky, because robot A is mounted to the ground. Just try some values and see if it helps or not. Therefore you have to use another tool with mass values.For example:
TASK PERS tooldata tTest:=[TRUE,[[0,0,0],[1,0,0,0]],[200,[0,0,500],[1,0,0,0],0,0,0]];
This one has 200kg at 500mm in front of flange.Another thing you could try is using a differen acceleration set. Look for AccSet.
0 -
Hello EricH, Thank you for your response.
I tried with the movement of the robots after disabling the motion supervision. To disable Motion Supervision, in the flex pendant only I followed: ABB -> Control Panel -> Supervision (Motion Supervision and Execution Settings) -> Set Path Supervision and Jog Supervision to OFF.
However, it did not make any change. I still get the Joint Collision error. The state of Robot A is "Brakes Released (with a separate 24 V supply)".
About the instruction SoftAC. Is it available in Flex Pendant? or in Robot Studio? As I do not have access to RobotStudio. Same for the ACCSet.
Besides, about mass I tried some values but it gives an error related to wrong tool definition.
I am sorry for asking basic questions, I am very naive with these robots. I am working on them from past three weeks. Also have no prior training with them. I am learning through the videos and tutorial available online.0 -
What are variant (model) of robot are you using?
200 kg may be more than the maximum payload of the robot of the robot.0 -
We are using IRB7600 325/3.10
Categories
- All Categories
- 5.6K RobotStudio
- 400 UpFeed
- 20 Tutorials
- 15 RobotApps
- 301 PowerPacs
- 406 RobotStudio S4
- 1.8K Developer Tools
- 250 ScreenMaker
- 2.8K Robot Controller
- 350 IRC5
- 74 OmniCore
- 8 RCS (Realistic Controller Simulation)
- 848 RAPID Programming
- 21 AppStudio
- 4 RobotStudio AR Viewer
- 19 Wizard Easy Programming
- 109 Collaborative Robots
- 5 Job listings