CNC touchprobe on Robotarm
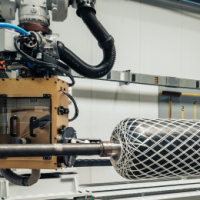
in IRC5
Hi All,
New to the Forum posting wise, but have come here often looking for answers.
we are currently working on a project to speed up and improve our userframe teaching method. Until now we have used the simple "pin in the robothead" with a 4+ point teaching of its TCP.
This has worked well enough for us in the past but we are moving into more precise processes and need to get more accurate results. And we want to have this in an (semi-) automated routine to help our integrators install the machines.
We've designed and built a simple tool to hold a CNC touchprobe in the robothead.
With this probe and a precise round steel sphere inside the robot's reach we attempt to calibrate the TCP of the probe.
We approach the sphere from several angles and at each angle we probe the sphere to find its relative centre location. Then after 4 of these points we use the mToolCalib function to calculate the new TCP of the probe.
However, we see a consistent 0.6mm mean error in the results. Do any of you have an idea where this might go wrong?
We are looking to teach the probe's TCP to within 0.2mm mean error.
Your input is much appreciated!
New to the Forum posting wise, but have come here often looking for answers.
we are currently working on a project to speed up and improve our userframe teaching method. Until now we have used the simple "pin in the robothead" with a 4+ point teaching of its TCP.
This has worked well enough for us in the past but we are moving into more precise processes and need to get more accurate results. And we want to have this in an (semi-) automated routine to help our integrators install the machines.
We've designed and built a simple tool to hold a CNC touchprobe in the robothead.
With this probe and a precise round steel sphere inside the robot's reach we attempt to calibrate the TCP of the probe.
We approach the sphere from several angles and at each angle we probe the sphere to find its relative centre location. Then after 4 of these points we use the mToolCalib function to calculate the new TCP of the probe.
However, we see a consistent 0.6mm mean error in the results. Do any of you have an idea where this might go wrong?
We are looking to teach the probe's TCP to within 0.2mm mean error.
Your input is much appreciated!
Engineer @ TANIQ
www.taniq.com
www.taniq.com
0
Comments
-
What is the diameter of the probe's tip?Lee Justice0
-
The tip is 2mm diameter, and the sphere we touch off on is 12mm in diameterEngineer @ TANIQ
www.taniq.com0 -
Did you mean that you use the instruction MToolTCPCalib? You wrote function mToolCalib and I cannot find that in the manual.
Where on the sphere do you touch off and finally, why a sphere instead of a point?Lee Justice0 -
Yes I'm sorry that is correct, MtoolTCPCalib.
We touch on several (11) positions on the sphere, and using those positions calculate a point in the middle of the sphere (with a least squares method).
Then we convert that point to a jointtarget, which will be one of the four inputs of the MtoolTCPCalib function.
We cycle through 4 positions with different orientations. each of which gives a calculated centre point of the same sphere.
The idea being that we can calculate the 'exact' same position like this, from different angles.
Engineer @ TANIQ
www.taniq.com0 -
I think that there is some data lost/errors induced on conversion from a "point" calculated to jointtargets. I also suspect that the rather small size of the sphere will amplify the error. This is just an hypothesis, but a larger sphere could be more forgiving, minimalizing errors.Lee Justice0
-
Thank you for the suggestion, we'll look at using a larger sphere.
Would physically moving the probe to a relative position, say 20mm above the sphere, and then getting the jointtarget using a CRobJ command be beneficial over the calculation method?Engineer @ TANIQ
www.taniq.com0 -
I really don't have an answer to that question, but I have a suggestion. Teach the TCP as one usually would and see if you get any improvement in the accuracy. This may help to determine if any improvement is even possible.Lee Justice0
Categories
- All Categories
- 5.6K RobotStudio
- 401 UpFeed
- 21 Tutorials
- 15 RobotApps
- 303 PowerPacs
- 407 RobotStudio S4
- 1.8K Developer Tools
- 250 ScreenMaker
- 2.8K Robot Controller
- 353 IRC5
- 74 OmniCore
- 8 RCS (Realistic Controller Simulation)
- 849 RAPID Programming
- 24 AppStudio
- 4 RobotStudio AR Viewer
- 19 Wizard Easy Programming
- 110 Collaborative Robots
- 5 Job listings